With demand outstripping supply, purpose build student accommodation (PBSA) is booming but delivery is not without its potential pitfalls.
The latest count of the purpose-built student accommodation (PBSA) sector in the UK paints a still significant imbalance between supply and demand.
The study published by property consultancy Savills in April, reveals that the UKs 20 largest student cities have a combined population of more than 1.3million full time students – but fewer than half that number of PBSA beds.
This according to Savills means that the student to bed ratio is currently 2.7 students to each available place. That could, however, become worse if up to 230,000 new PBSA beds aren’t delivered.
No wonder then that the latest Glennigan construction Review reveals a buoyant PBSA sector with student accommodation schemes worth £502m in the first quarter of 2024 alone – arise of 34% on the same time last year.
It means that in all student accommodation now accounts for 5% of total housing starts. Glennigan predicts by the end of this year new starts in total will be up 16% on 2023, with a further increase of 10% forecast in 2025.
The challenge in supply of purpose-built student accommodation
“The main challenge for the sector other than delivering enough of it, is finding suitable sites for PBSA schemes”, says Paul Stevens, Managing Director, Acorn Aluminium.
“While there are lots of out-of-town campuses many of the most established subscribed to universities in London, Bristol, Manchester, Glasgow, are in city centre locations, which means PBSA schemes also need to be in central locations.
“That pushes development to brownfield sites, which invariably come with a number of specific challenges.”
This includes footprint. City centre locations often have limited access, which creates challenge for the supply chain, increasing the importance of just-in-time supply.
Acoustics also assume increased importance. “Again, city centre locations and multi-use schemes mean that sound insulation is important”, Paul says.
“It reflects an increased focus on acoustic performance in general in schemes on brownfield locations.”
“We’ve worked in partnership with main contractors across a number of projects to deliver effective acoustic specifications as well as to overcome challenges I location through just-in-time delivery and increased stock holding ahead of time in our warehousing facility.”
Fusion Students Sheffield
Located in the heart of Sheffield and ideally located for students at the University of Sheffield and Sheffield Hallam, Fusion Students, is a four block 846-unit student accommodation scheme.
The site off Fitzwilliam Street. Is defined by a graduated profile, ranging in height across the four blocks from six-storeys at its lowest elevation to 17-storeys. This incorporates high end-communal facilities across ground and mezzanine levels including a cinema, gym and break out areas.
The £46.5million scheme makes significant use of commercial glazing. Supplied manufactured and installed by Acorn Aluminium, this includes two-storey curtain walling, bringing light and a sense of space into communal areas; and 1,150 windows.
The project, designed by architects Corstorphine & Wright, was completed in summer 2021.
Our approach
Acoustic specification was cited as a key part of the brief. The development is located in the heart of Sheffield’s bustling city centre, with much of the development facing a busy, and potentially noisy street.
Working with the architects, ISG, and acoustic consultants, we developed a dual specification of standard and acoustic energy efficient IGUs.
The latter were installed in those areas exposed to greatest noise including roadside and at lower levels. These were manufactured from a combination of 8.8mm acoustic laminates and 8mm toughened glass to achieve to achieve a Sound Reduction Index (RW) rating of 43.
We balanced the requirement for a high degree of sound insulation in these outwardly facing elements of the building with RW ratings of 32 and 38 in other areas of the building less exposed to street noise.
Combined with aluminium commercial windows manufactured in the SPW600 system from Senior Architectural Systems, we were able to develop, manufacture and install the window element of the scheme to deliver advanced acoustic performance in those areas where it was required, but to support cost-effective delivery by avoiding over-specification of performance elsewhere.
Vita Student Nottingham
As a leading provider of student accommodation, Vita Students operates nationwide, adding Vita Student Nottingham, to its list of locations in October 2020.
Part of the regeneration of Nottingham’s southside, the 319-room accommodation block is situated in easy reach of Nottingham Trent University and the University of Nottingham and a stones’ throw from the City’s train station.
Designed by architect Fuse Studios Limited and delivered by main contractor Morgan Sindall, the 101,375 square foot development the contemporary build is split into three tiered towers of six, eight and ten storeys each.
There’s also a 6,000 square ft communal hub space for co-working and socialising, complete with a coffee bar, separate study rooms and private, bookable lounges.
Acorn Aluminium was appointed by Morgan Sindall Construction to design, manufacture and install, windows, panelling and louvres, into the £24million scheme.
Given the location of the site within in metres of tram and railway lines, the brief included a specific focus on acoustic insultation.
Our approach
Supplied in RAL7006 Beige Grey, open-in casement windows were manufactured by us in the acoustically rated and tested Technal FY65 aluminium commercial window system.
Installed in a stacked formation across sequences of two-storeys, they also featured louvre grills, sitting under panels, used to face floor levels, to provide background ventilation.
We also developed a dual specification of standard and acoustic energy efficient IGUs, which were installed in the acoustically rated and tested Technal FY65 aluminium commercial window system.
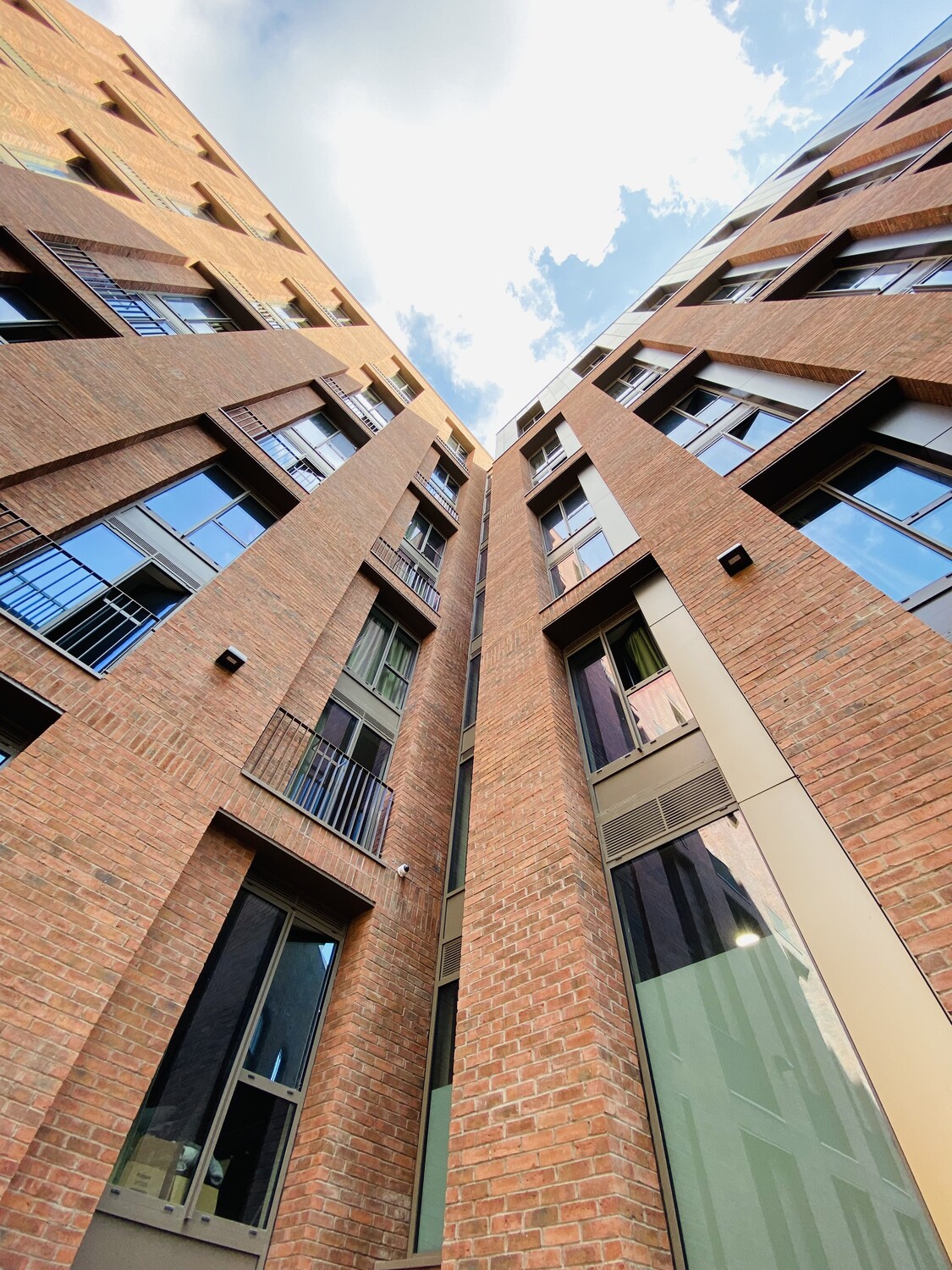
This meant that combined with high performing units manufactured in 8.8mm acoustic laminates, 18mm cavity and 6mm toughened glass, we were able to achieve a Sound Reduction Index (RW) rating of as high as 42dB.
This specification was used on those elevations exposed to potential noise from the street and transport networks, with installations on less noisy elevations achieving RW ratings ranging from 35 – 39dB RW.
Argon-filled and with a centre pane u-value of 1.0W/m2K, the combined window and unit u-value was an ultra-energy efficient 1.3W/m2K.
For more about Acorn Aluminium please call 0115 928 2166, email [email protected] or visit www.acornalumnium.com